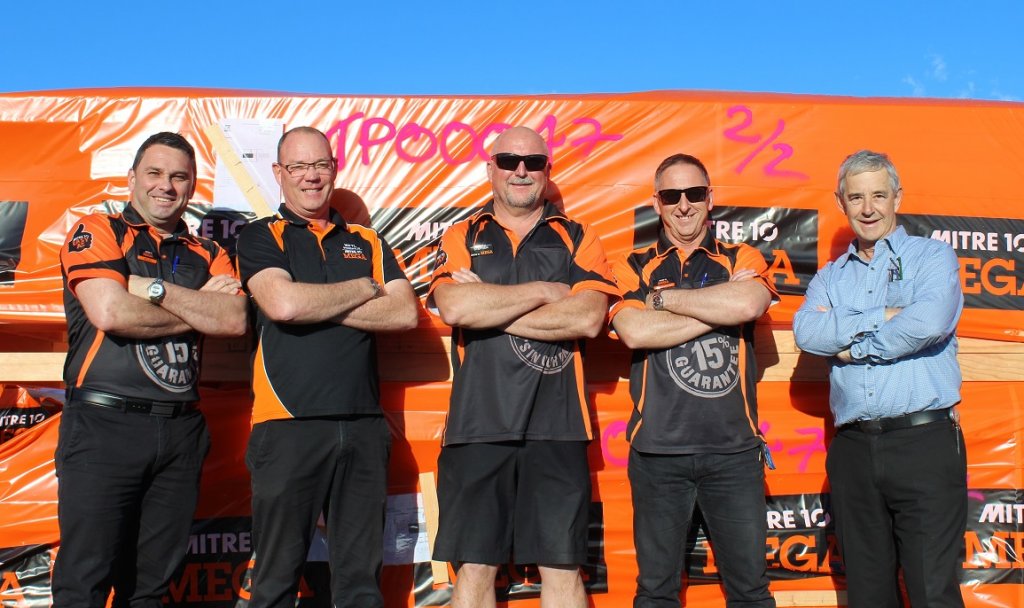
From left, Director Myles Whitcher; general manager, Doug Payne; director Stephen Deverell; director Brendan Lafferty; and director Terry Wilson at the launch of the new factory.
A state-of-the-art new frame and truss factory had its official opening in Hautapu recently.
Around 20 stakeholders and guests donned safety gear and took a tour of the Waikato Frame and Truss plant, getting a crash course on the ins-and-outs of house framing in the process.
Set on an 11,000m2 site, the factory employs 22 workers and supplies house framing and trusses to the Waikato and South Auckland exclusively for Mitre 10.
It’s a far cry from the previous operation which started in 2013 and ran out of the killing floor of the old Affco meat works on Matos Segedin Drive, originally employing four people.
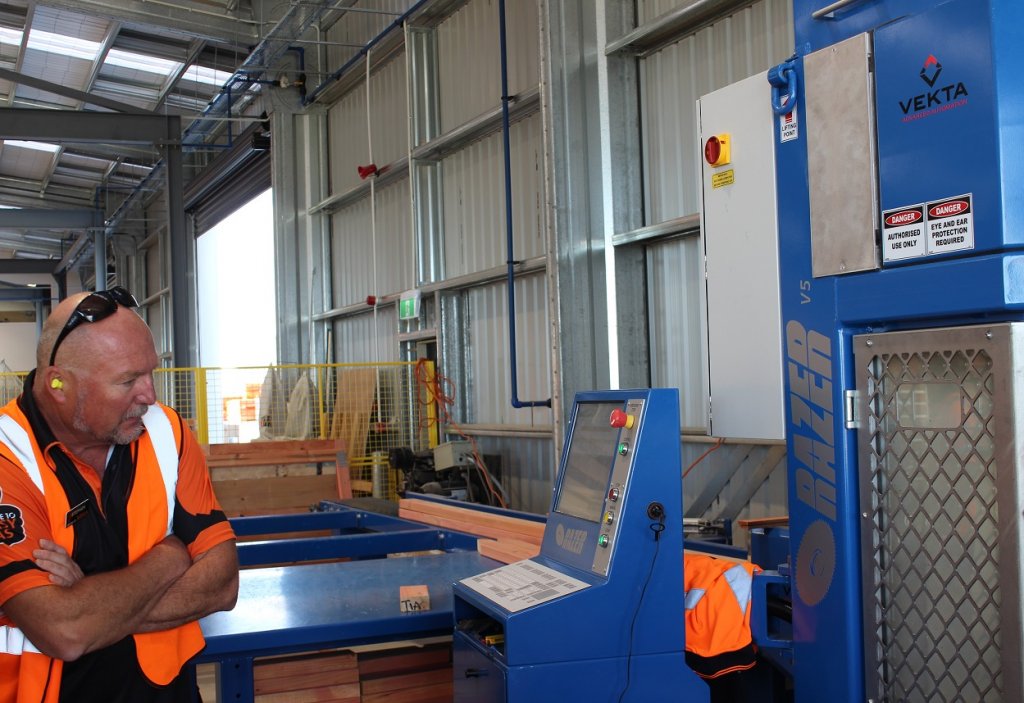
Stephen Deverell checking out the Razer V5 linear saw.
“It’s a huge step up for us to come here and do this,” said one of the venture’s four directors, Stephen Deverell, co-owner of Cambridge Mitre 10 Mega. His Cambridge store co-owner Brendan Lafferty is another director, along with Myles Whitcher and Terry Wilson from Hamilton. Terry said the operation would not have gotten off the ground without Brendan and Stephen. “We are happy to be partners with the Cambridge boys,” he said, adding that the town is the ideal location for the plant due to the proximity of the Waikato Expressway.
Work on the new factory started in August 2016, and the result is a 1600m2 factory floor with offices upstairs.
Precision is vital in the operation, with each house having between 3,000 and 4,000 individually cut pieces in its framing and trusses. House plans are detailed into CAD software which works out exactly what needs to be manufactured.
The plant has invested in new technology, Sapphire, that allows for plans to be made into a 3-dimensional model, so builders and clients can see exactly what the house will look like. The 3-dimensional model can go onto phones and devices, making it more accessible than a 2-dimensional laminate to the builder. If there’s a query, a phone can be pointed at part of the frame or truss to make sure everything is in alignment. “You can line up with the frame and go in real time with the phone to see that each piece is fixed properly,” explained the factory’s general manager, Doug Payne. By early next year it is expected that all frame and truss jobs will go through Sapphire, making this one of the only factories in the country to fully adopt the programme.
Once the plans are put into the design software, they are inputted into the factory’s new Razer V5 linear saw. The Razer then cuts the pieces in the most efficient way, rather than cutting them in order, resulting in a considerable reduction in waste offcuts on the site.
“It’s taken the human factor out of cutting, making it more accurate and safe,” Stephen said.
Printed with a job and component number as they go through the Razer, the pieces are then assembled and put into the right order, ready to be delivered to building sites across the greater Waikato and South Auckland.